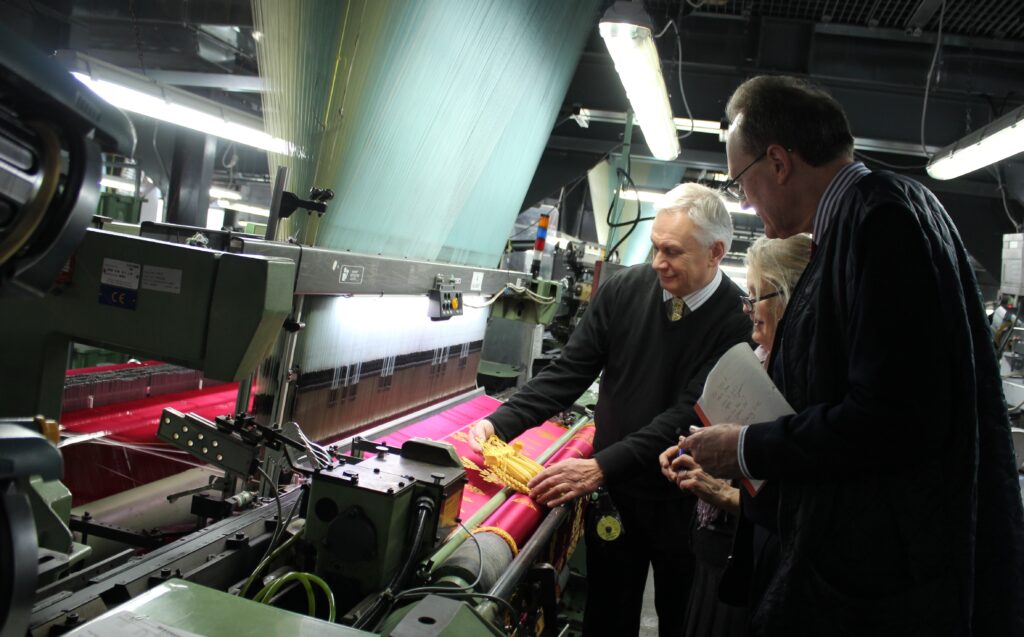
Weaving Heritage
Humphries Weaving is located in Sudbury, Suffolk, where the heritage of weaving dates back centuries. The silk weaving industry, established in the 17th century, was originally based in Spitalfields, Bow, and Bethnal Green in London. In the late 18th and early 19th century, weaving operations moved away from this area to avoid the restrictions imposed by the Spitalfields Acts. Weavers settled in towns such as Braintree, Halstead, and Sudbury, on the Essex and Suffolk border, thereby creating a hub of excellence for silk fabric woven in East Anglia.
1130
‘Weave truth with Trust’
The Worshipful Company of Weavers is the oldest Livery Company in the City of London that was established in 1130, and may have been formed even earlier. The company received a Royal Charter in 1155 and still has ties to the textile industry today.
Today the company focuses on Weaving, charity, and fellowship continuing to fulfil its role of support for the art and skill of weaving whilst actively helping to improve society.
Both Richard Humphries and Natalie Mumford are active members of the livery and its textile committee and in 2016/17 Richard became the 888th Upper Bailiff of the Company.
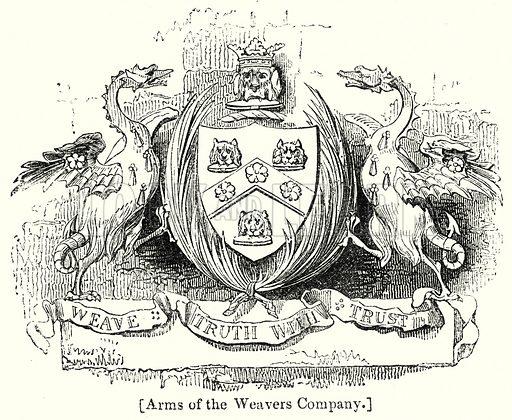
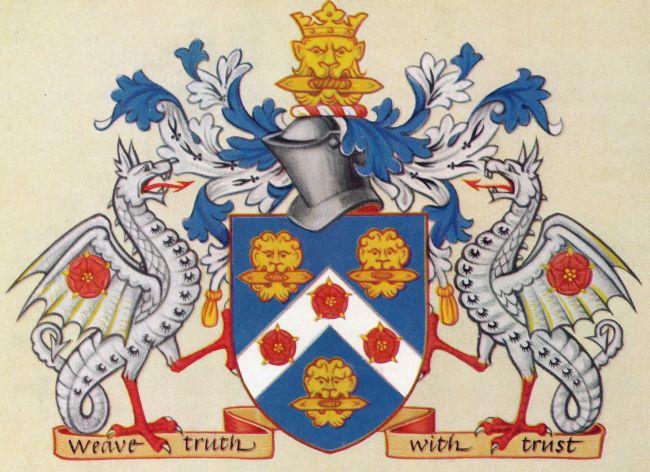
1801
Jacquard Looms
In 1801 a Monsieur Joseph Jacquard of Lyon France first demonstrated a device that could be fitted to a loom to create patterns automatically, using hooks controlled by punched paper cards to lift specific groups of warp threads. Over succeeding decades this technique became widely adopted, replacing old draw looms and revolutionising the craft of silk weaving. In essence the Jacquard system represented the first ever ‘computer’.
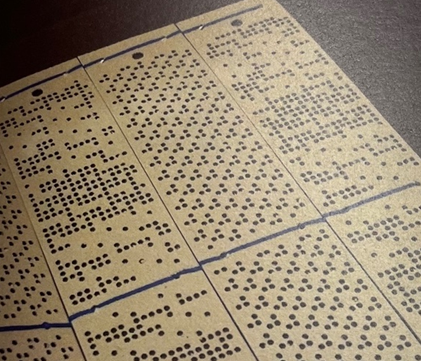
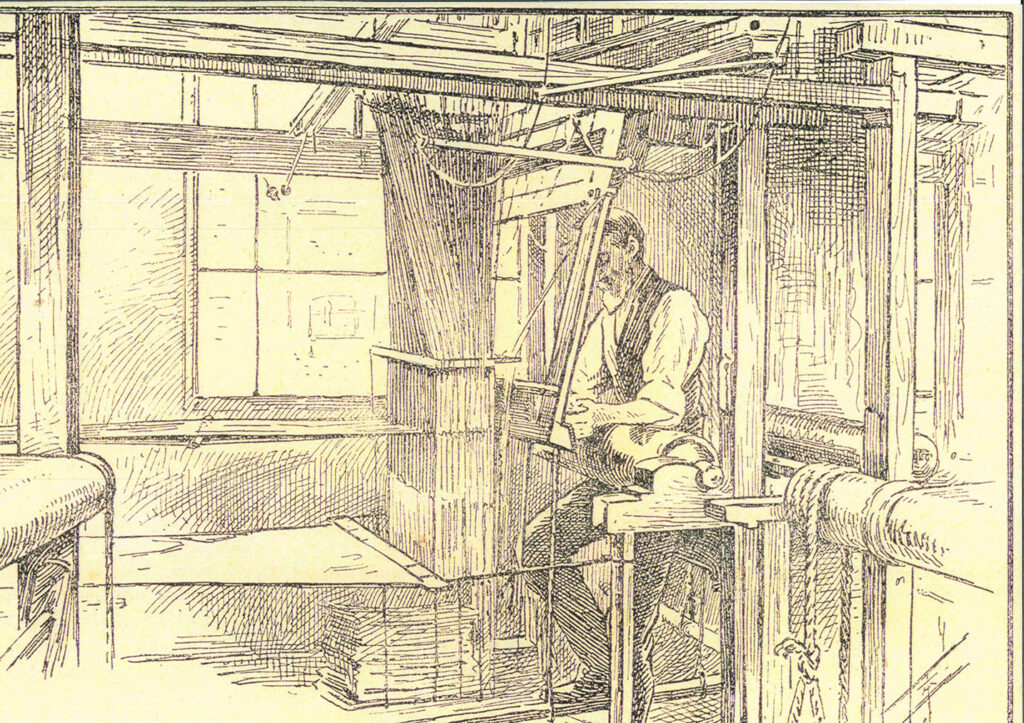
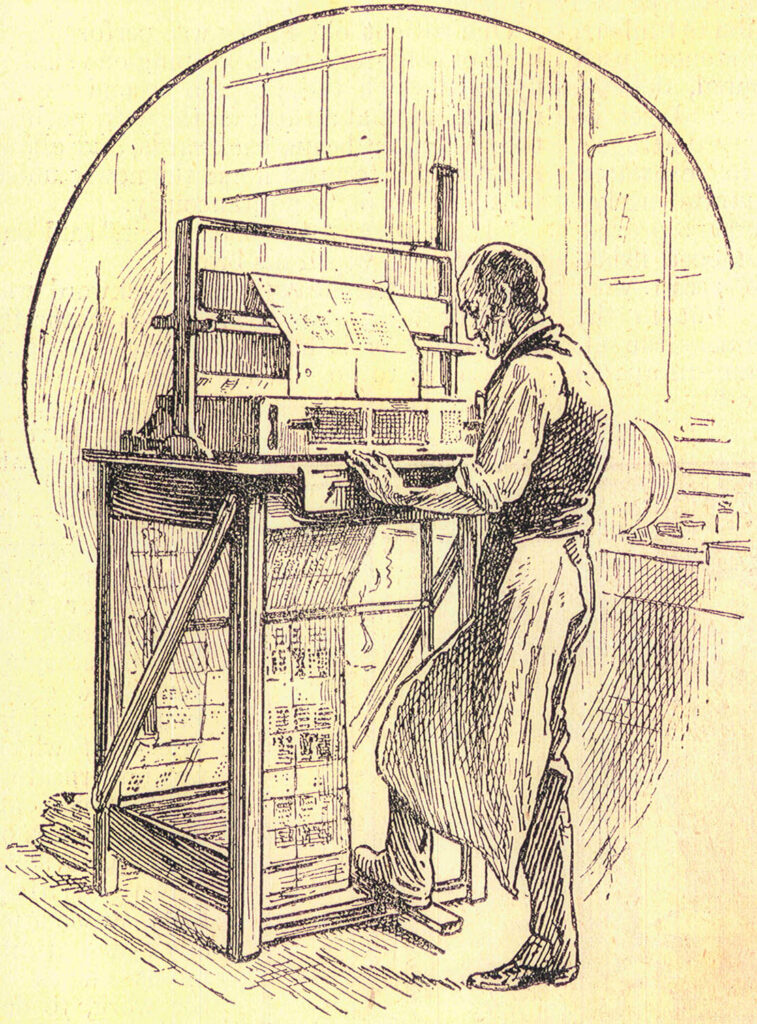
1960s
Richard Humphries was a creative child, excelling in artistic and musical endeavours but keen to move on from the constraints of school. At the age of 14 he began a weaving and design apprenticeship at local silk weaving firm Warner & Sons, Braintree. This was to be the last full apprenticeship for the company and under the tutelage of Frank Davies RCA, Richard was trained in; silk throwstering, technical aspects of warping, weaving and handweaving, design, Jacquard card cutting and sales. One of the more unusual aspects of the training was elocution lessons to help with presenting to clients, soon Richard was exploring the design worlds of London and Paris.
Warner & Sons dated back to 1839 in Spitalfields, later going on to acquire Daniel Walters silk weaving firm in 1894, which included its factory site of New Mills, Braintree. Warner & Sons remained there until its closure in 1971. An original Daniel Walters loom that Richard J. Humphries restored in 2024 can now be found on display and in working order in the Sudbury Silk Mills shop.
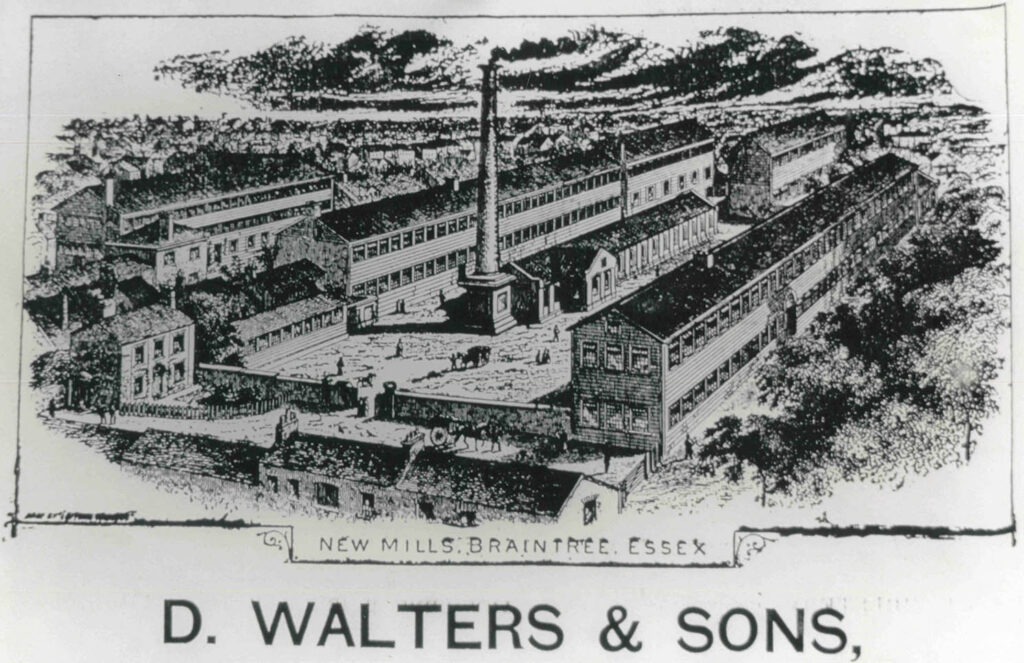
1970
Ashburton Lodge, Sudbury
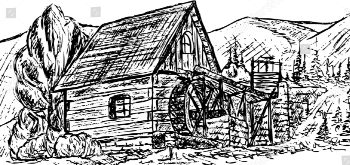
Richard Humphries was enjoying life between the design studio, the London offices of smart interior decorators and visits to Royal locations, brimming with excitement and with a promising career ahead of him when Warner & Sons announced their closure in 1971.
“I received fifty pounds redundancy, and my first thought was to travel to India with my guitar, but my uncle encouraged me to take the chance and set up my own weaving company at the young age of 20. Slowly I made offers to purchase designs, Jacquard cards, books and equipment. £1 for a loom if I took it apart and moved it myself and I was rescuing things from the skip.”
Richard was further supported in setting up by his mother and father, who provided both encouragement and much needed storage space. Peter Walters, of nearby Sudbury weaving firm Stephen Walters & Sons (founded 1720) offered him space in the basement of Ashburton Lodge, Sudbury Silk Mills, to set up dobby looms and The Humphries Weaving Company was born.
Securing workspace led to support grants from the Crafts council and the Worshipful Company of Weavers. Robert ‘Bob’ Mears, a redundant Warner & Sons weaver volunteered to join, without pay initially, happy to ‘square up’ when orders were converted and they began weaving. The orders did come and the early orderbook contains fabrics for Jon Bannonberg, Sibyl Colefax & John Fowler, Chester Jones and Radar cloth for the MOD. An early innovation was to weave window blinds encapsulating mirror squares in the structure. The decorative finish was specified for the newly built Penta Hotel in London in 1973 which boasted 902 bedrooms and cost £100million to build.
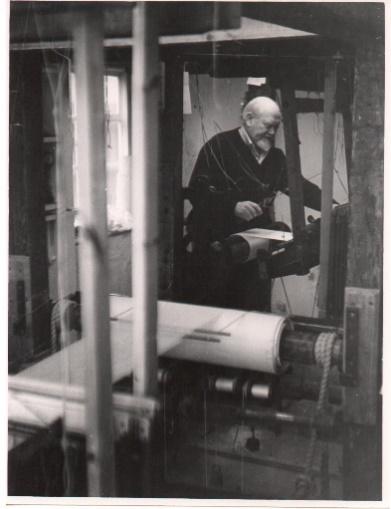
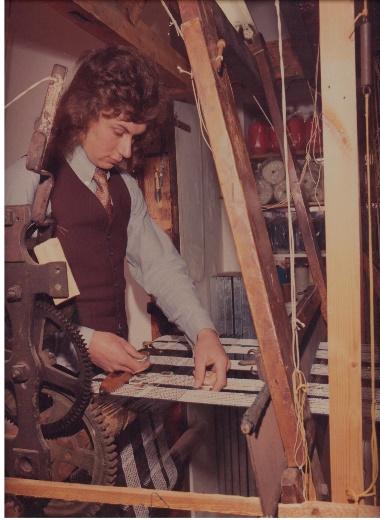
1975
DeVere Mill, Castle Hedingham
Humphries Weaving quickly outgrew the space at Ashburton Lodge and moved to the old school at Castle Headingham, renaming the building DeVere Mill. The space and high ceilings allowed for Jacquard looms Richard had saved to be put into operation.
Humphries Weaving were able to start weaving legacy patterns for Royal Palaces, Historic Houses and the National Trust. What started as a very small operation, soon become a highly prestigious and renowned silk weaving company; designing fabrics for some of the most important interiors, in Britain and abroad.
Later, Richard’s work at Hampton Court and the Royal Palaces, restoring the State Apartments was to be recognised through the award of an MBE for his services to the textile industry.
Royal commissions were to follow and the Queen’s Silver Jubilee gave the business an opportunity to gain in reputation as the State Gold Carriage was reupholstered along with the Green State Drawing Room at Buckingham Palace for the Royal Palaces. The National Trust and other major institutions followed and when a 56 inch wide brocatelle was ordered for the Speakers Bed in the Palace of Westminster, the greatest challenge was to recreate the loom for it. The result was to re-establish the ability to recreate such complex structures once again.
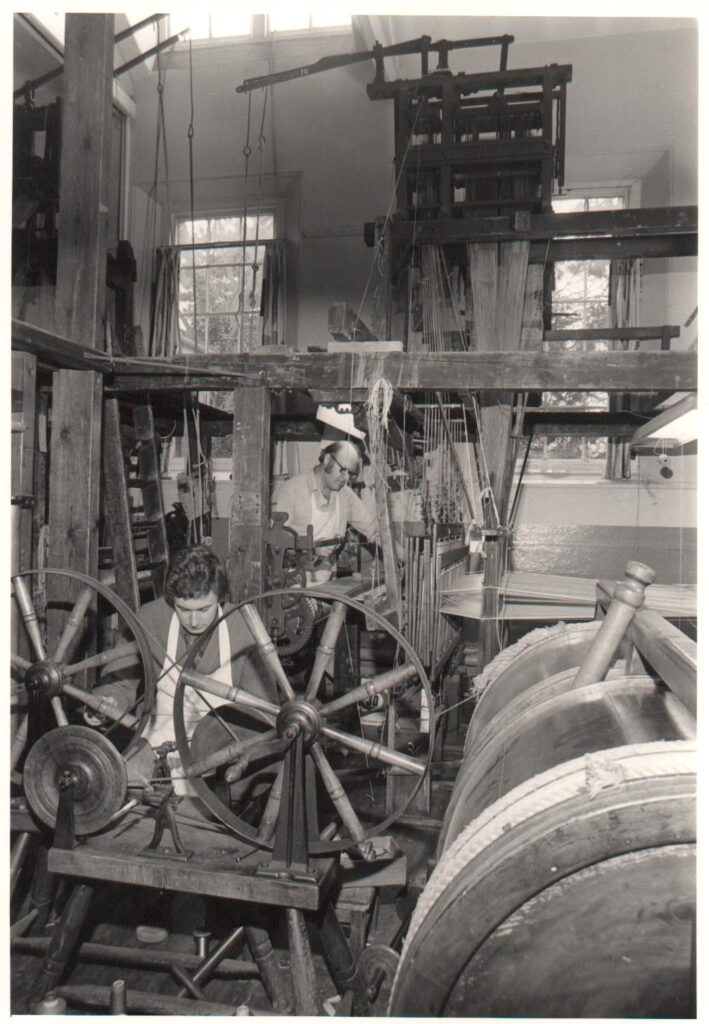
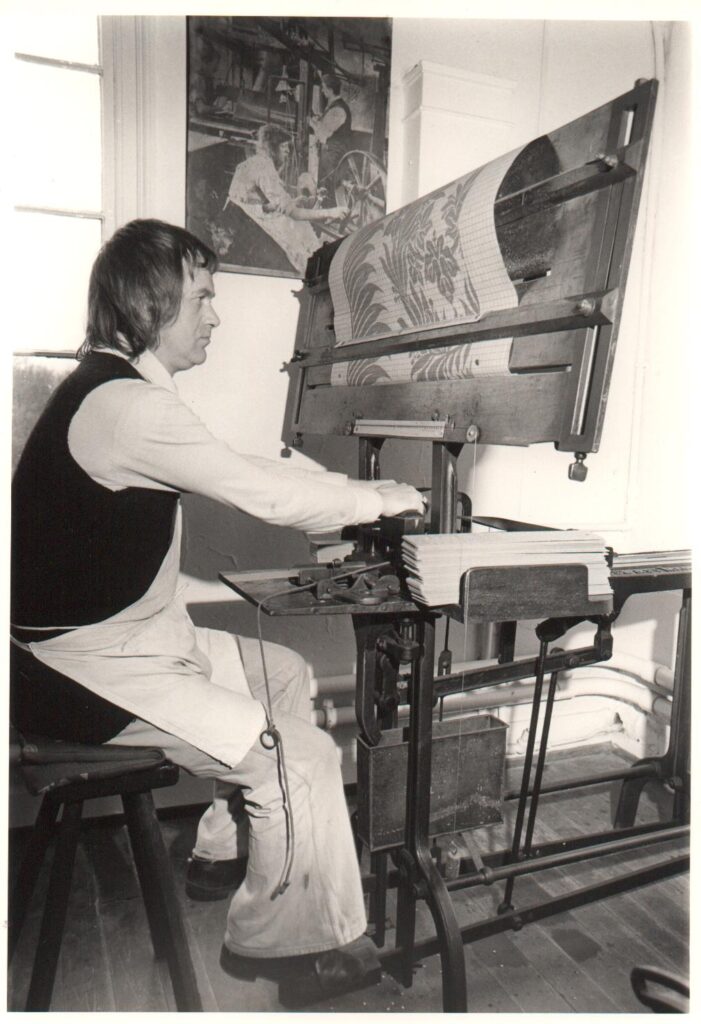
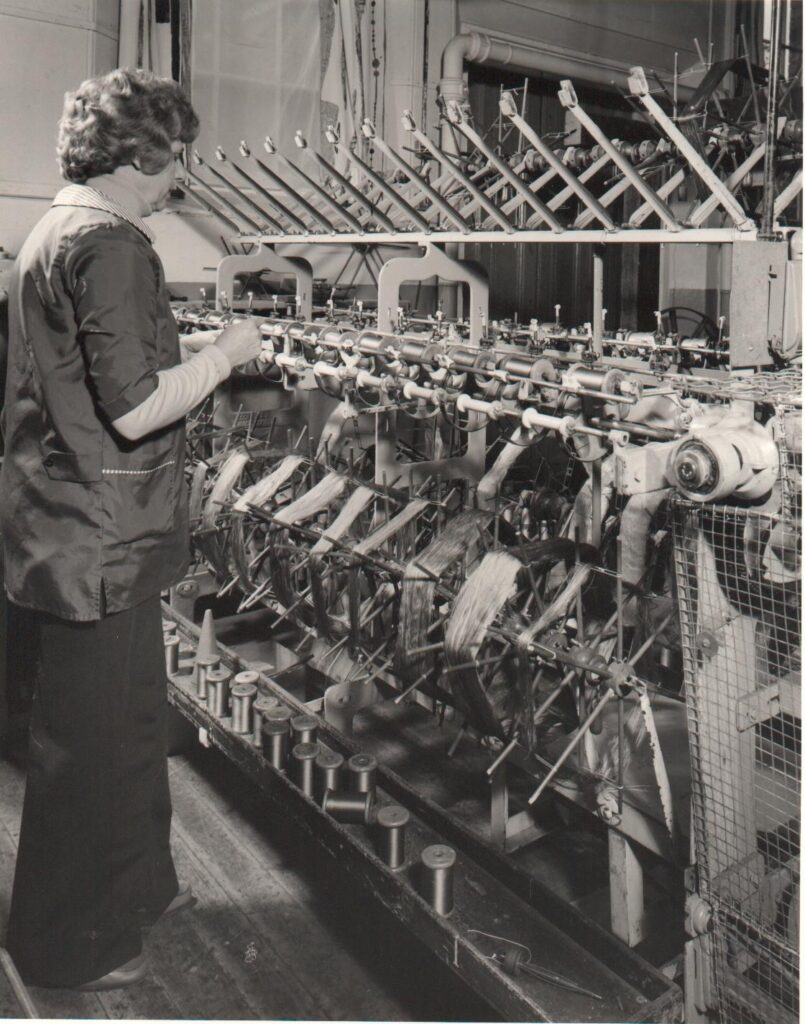
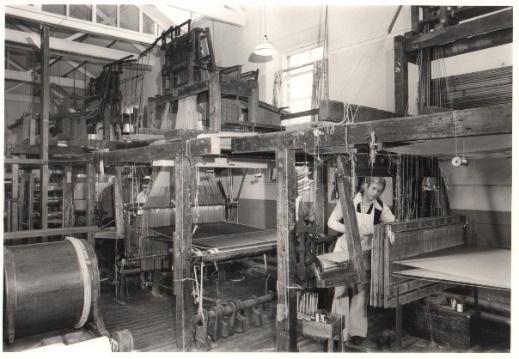
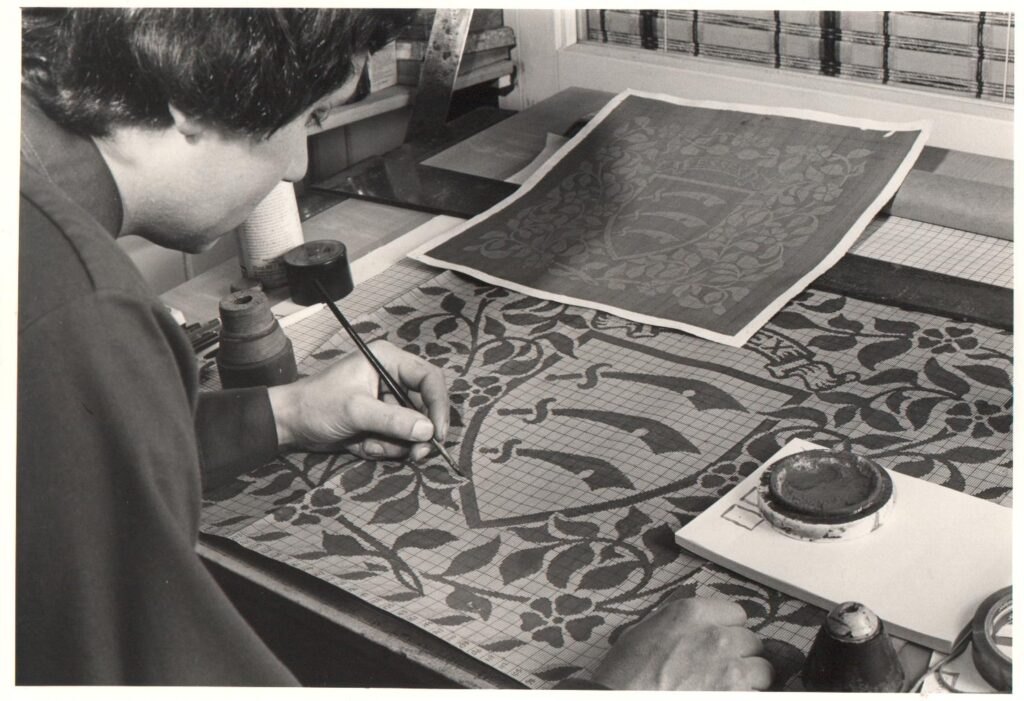
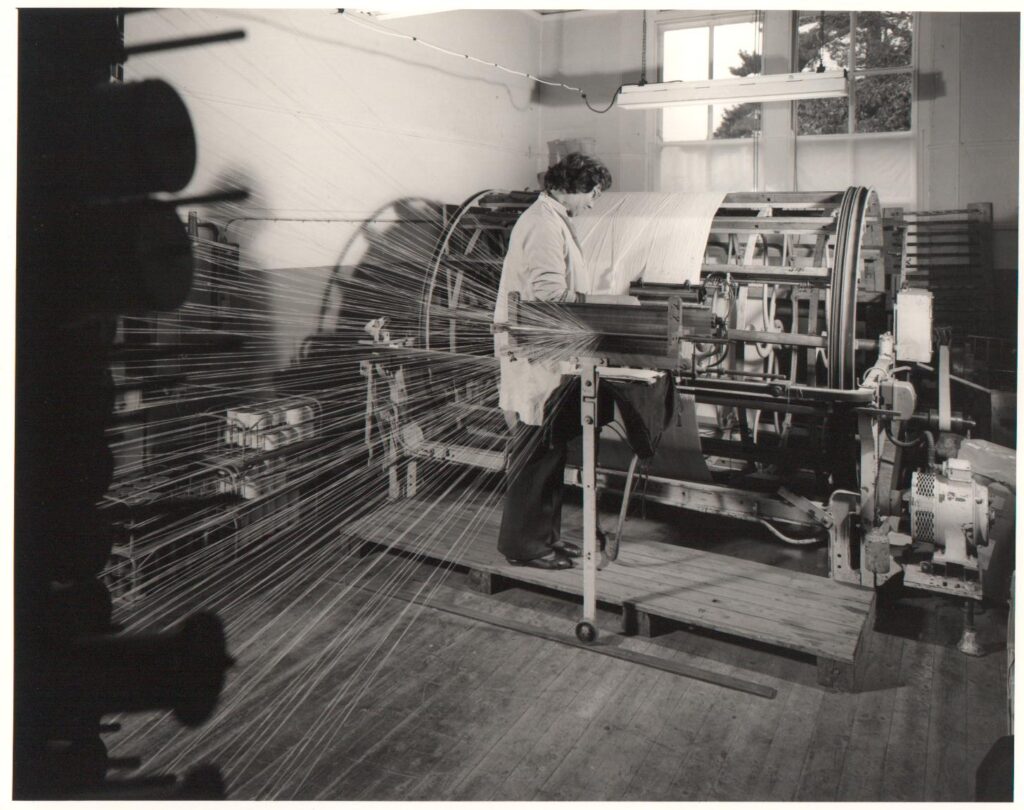
1980s
In 1985 all efforts in his field were rewarded when Richard received an MBE from the Queen for his services to the textile industry. It was a busy year when a proposal to build a working museum in Warner’s former Mill was approved and the decision to press on for opening at the turn of the decade.
This was to coincide with the terrible fire at Hampton Court Palace, which devastated the Kings Apartments. This led to an intense period of research and recreation to reinstate bespoke fabrics for the restoration.
BBC Sounds; The Reunion (Windsor Castle Fire)
The decade contained other major restoration programmes for Ham House, the Palace of Westminster Speakers Apartments, Queens House Greenwich and the Metropolitan Museum of Art, New York. With the demand for fabric increasing, more loom building was needed to keep up with deliveries. With the planned increase in museum space the business was well placed for development.
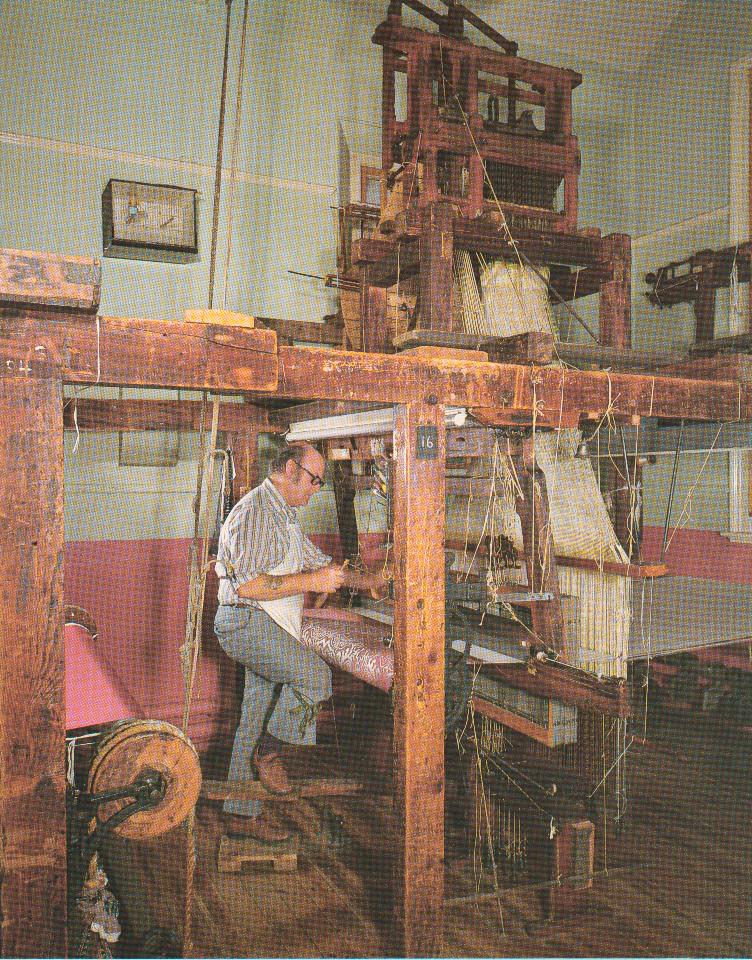
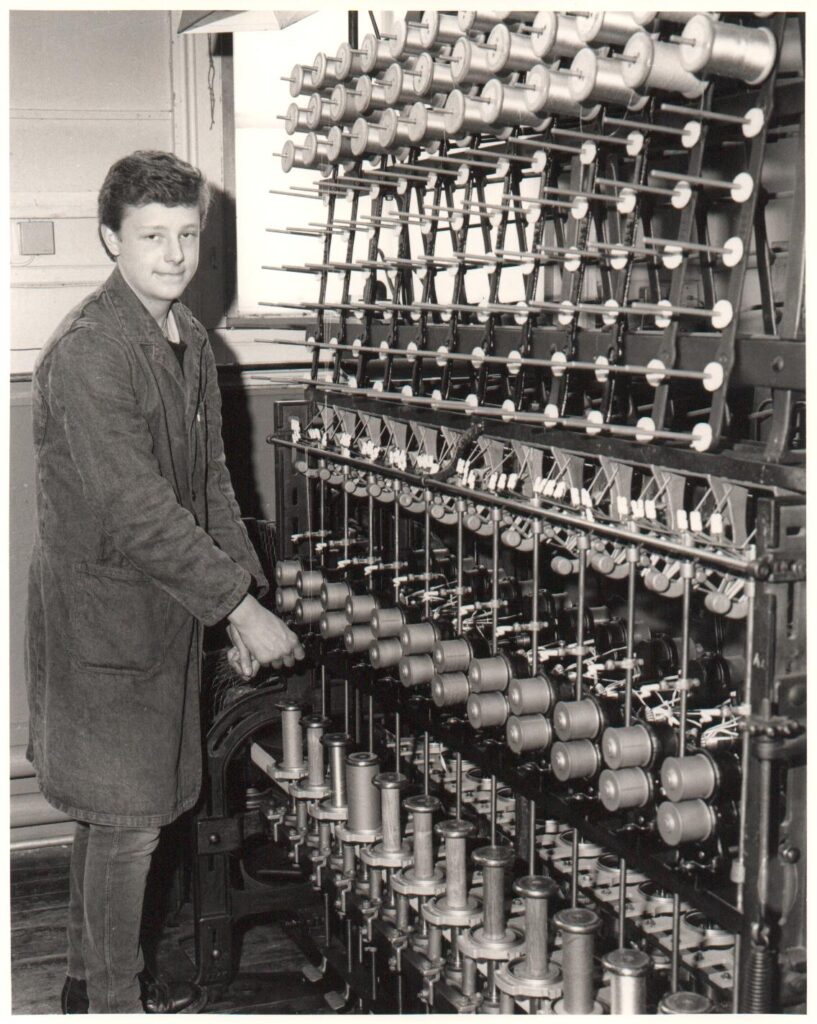
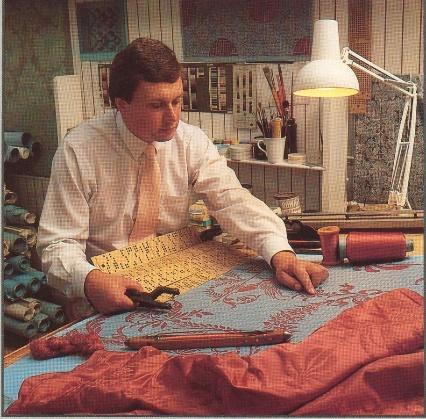
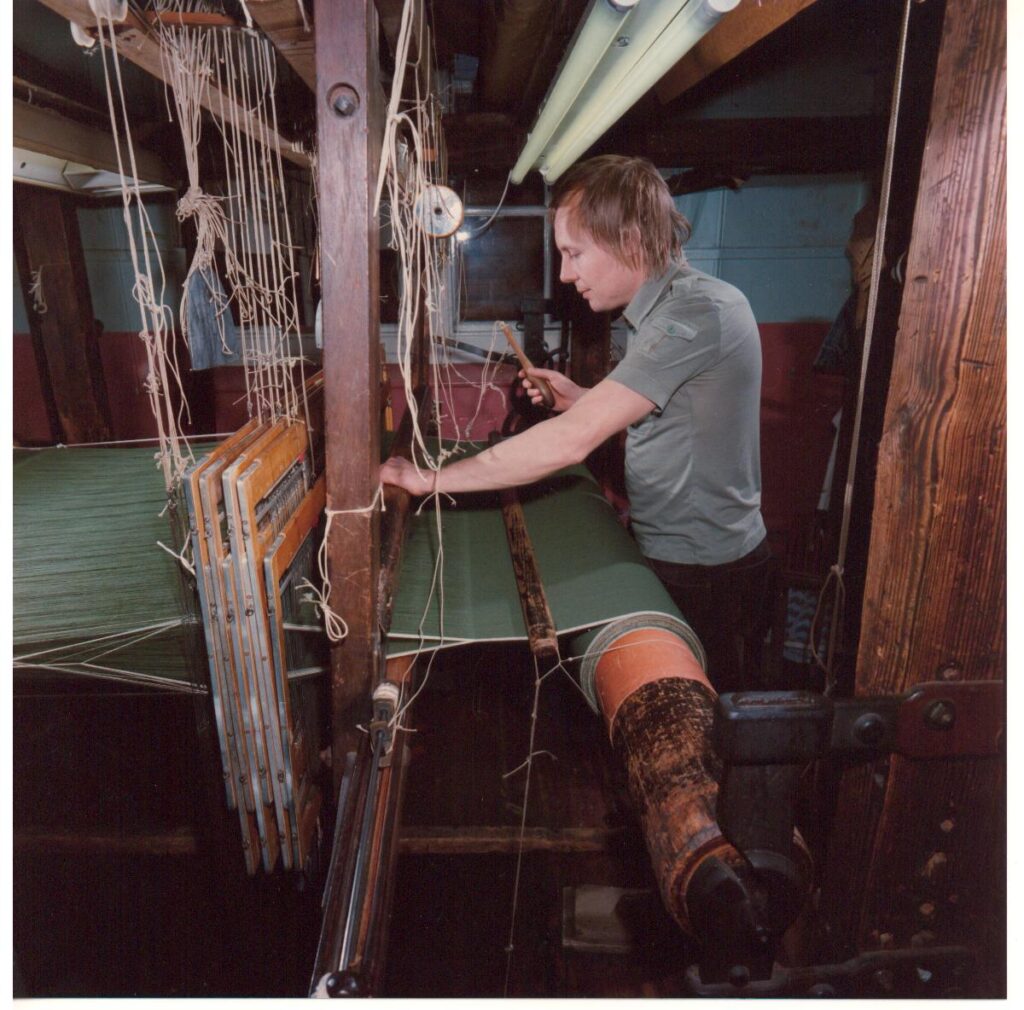
1990s
New Mills, Braintree
The weaving company had 18 month’s work booked in advance and the museum received 70,000 visitors in the first 12 months. This also meant an up-turn in staff levels rising to 23 employees. With ten looms at New Mills and a further six at DeVere Mill the variety of cloths available gave the business a leading edge in custom cloth for decorators and designers. There was space at DeVere mill to build a new dye house for specialist colours.
In 1992 another devastating Royal Palace fire took place at Windsor Castle where Richard had already spent years reweaving damask for several rooms. Again, Humphries Weaving used their archive and access to the palace team to research and recreate multiple bespoke fabrics for the restoration of the State Apartments.
Alongside this body of work historic recreation commissions were received for Spencer House, Kensington Palace, Apsley House and Kedleston Hall and London wholesalers were taken on in order to relieve pressure on decorator cloth sales allowing Richard to concentrate more on the making of historic fabrics required.
The volume of business led to developing a silk throwstering floor at DeVere Mill to give a vertical manufacturing ability from raw silk to made-up product for retail. This activity was requiring attention on the two sites which were nine miles apart so there was a daily delivery from one to the other which included transport for employees. By the mid-1990 the business was really at a very critical point where both sides of the business of tourism and fabric manufacturing were at full capacity.
At this same time the silk market took a massive hit when China lowered its prices so low as to render all throwstering in the UK a non-viable activity. When the price reached half of what it was, this meant the end of the making of silk thread for Richard and with his lease up for revision at New Mills it was time to condense the activity into DeVere mill once more.
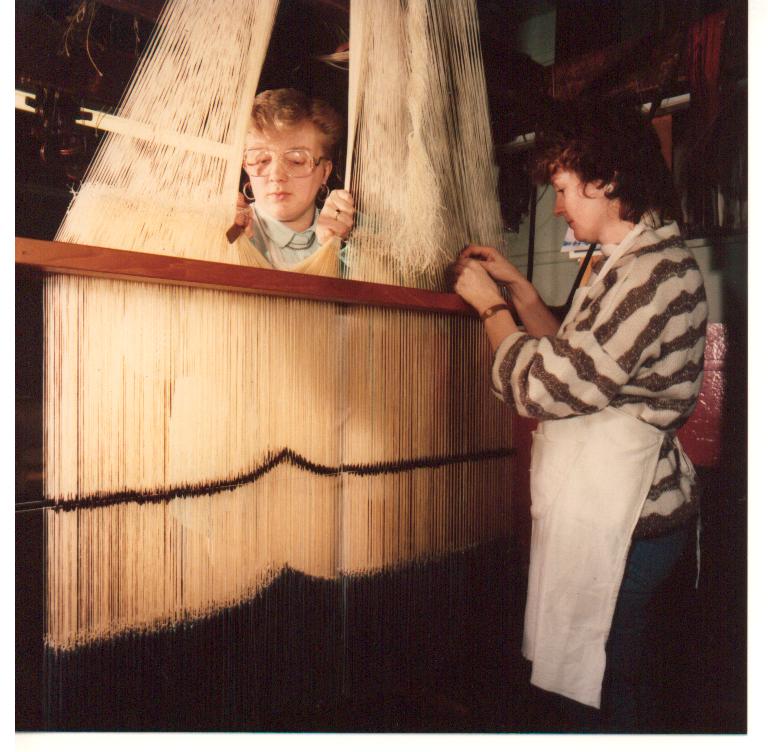
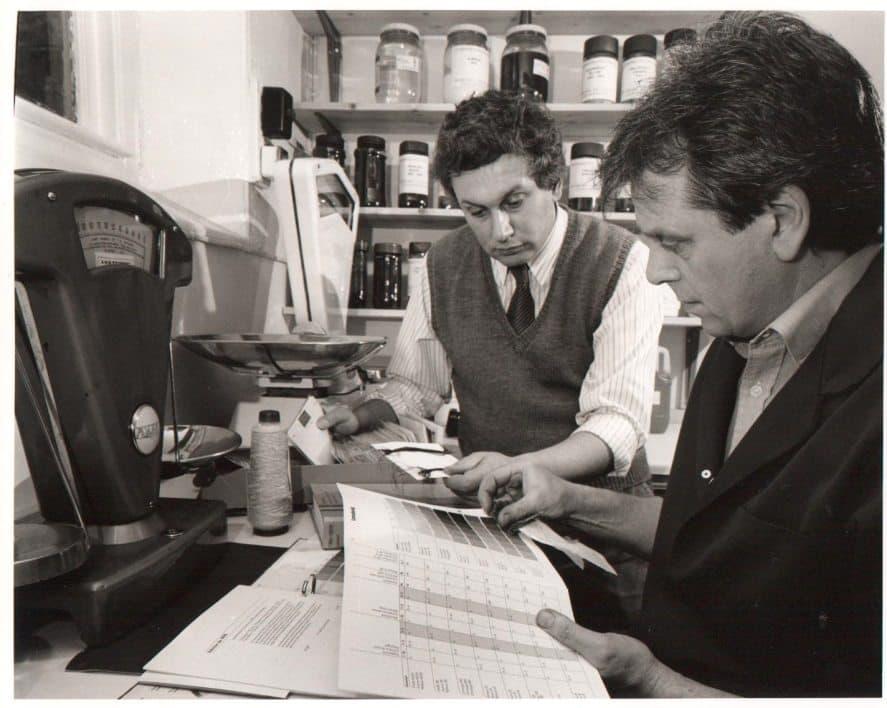
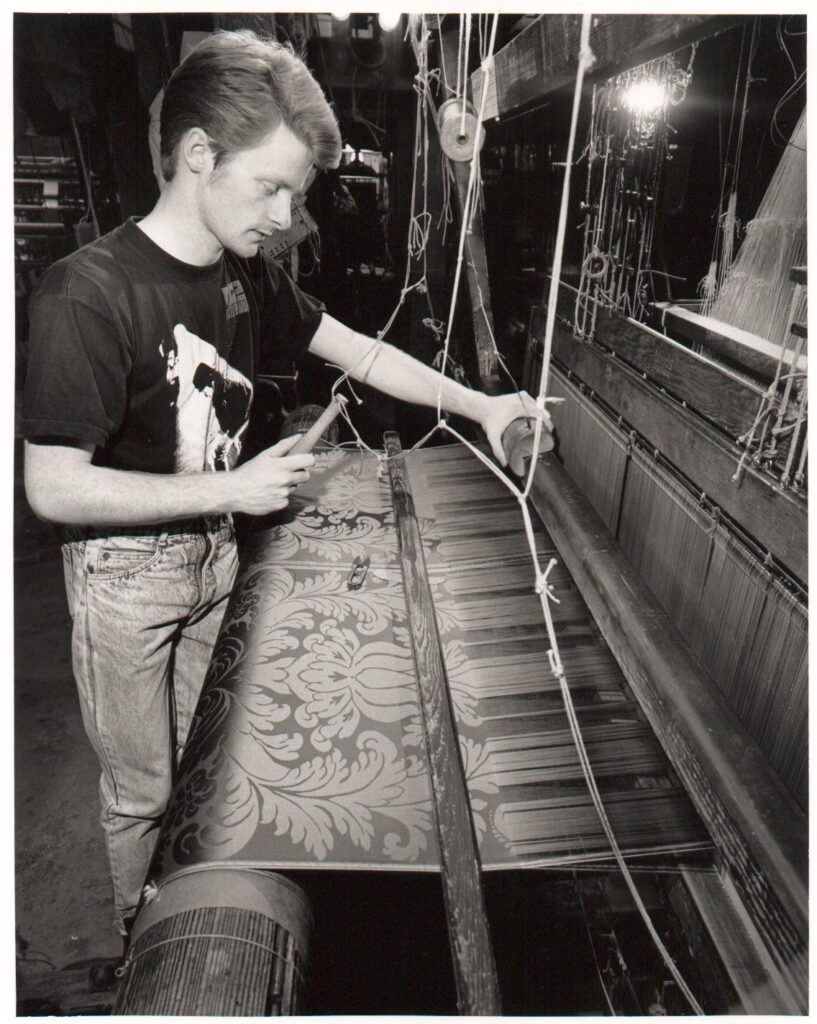
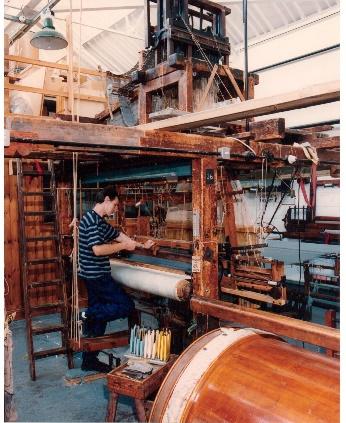
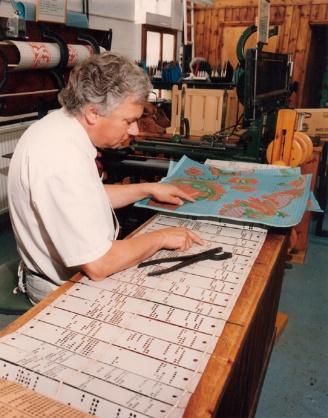
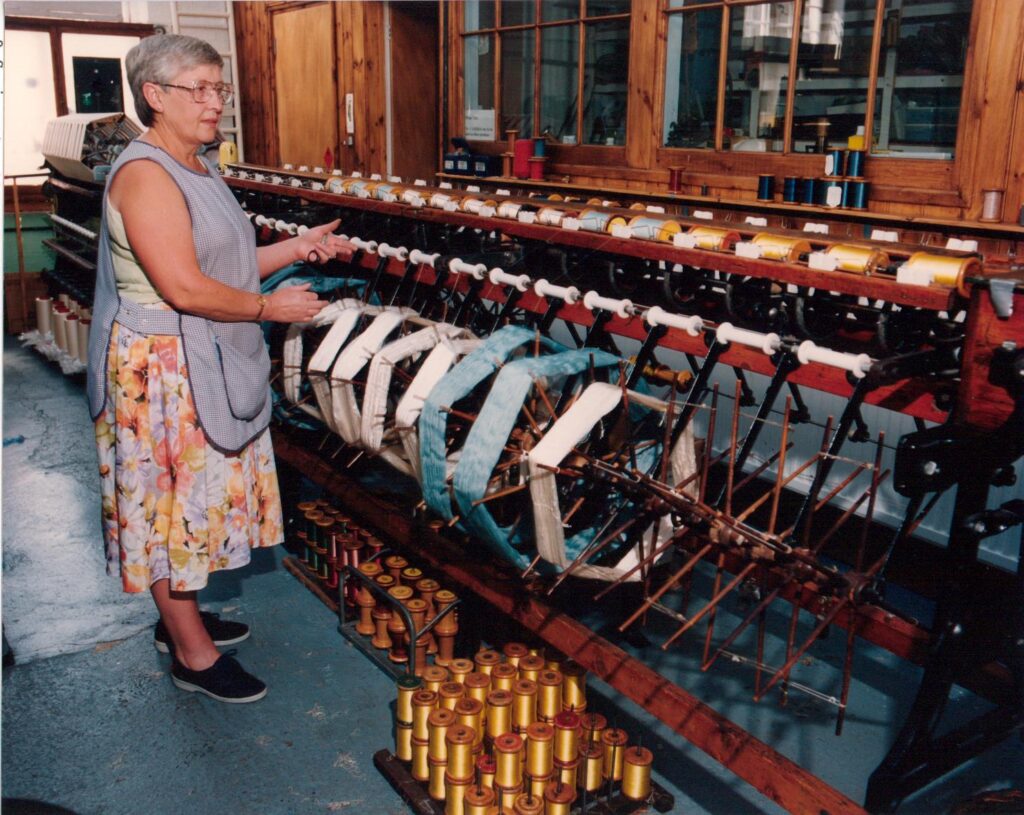
2000s
Full circle return to Ashburton Lodge, Sudbury Silk Mills. As the millennium turned, the planned restoration of Osborne House meant the firm had its greatest challenge to face. The Amber Room at Osborne House required a most complex design damask on an extra wide harness requiring a treble Jacquard head on the loom. Although the business had the machine and equipment it would require Richard’s skills to rebuild the Jacquards, harness and loom before re-drafting and cutting the Jacquard cards to make the design. The whole project took over two years to complete which culminated in Richard meeting the Queen at the re-opening of the house.
With the growing success of the reputation of the firm the company now needed to move forward and seek investment for machinery upgrades. The looms would need replacements and new staff training would challenge the quest for modernisation. In 2004 a major decision taken was to move back to their original premises at Sudbury in Suffolk. Here was the opportunity to upgrade the firm’s weaving ability at Sudbury Silk Mills and invest in more efficient weaving. The looms were soon making new wall coverings for Windsor Castle and the National Trust, adapting the technology and innovating techniques to deliver expert fabrics. The “special, unusual and unique” were all taken on in making the Humphries brand synonymous with quality and attention to detail. The weaving floor today runs over 40 high speed rapier looms, as well as retaining onsite dyeworks and finishing capabilities.
As business grew further, Richard expanded his sales and design team for the first time to began passing on his skills and expertise to the next generation of account managers. This move away from wholesale/agent representation in London and the US suited the bespoke nature of the projects that Humphries are renowned for and allowed them to give the care and support to their customers.
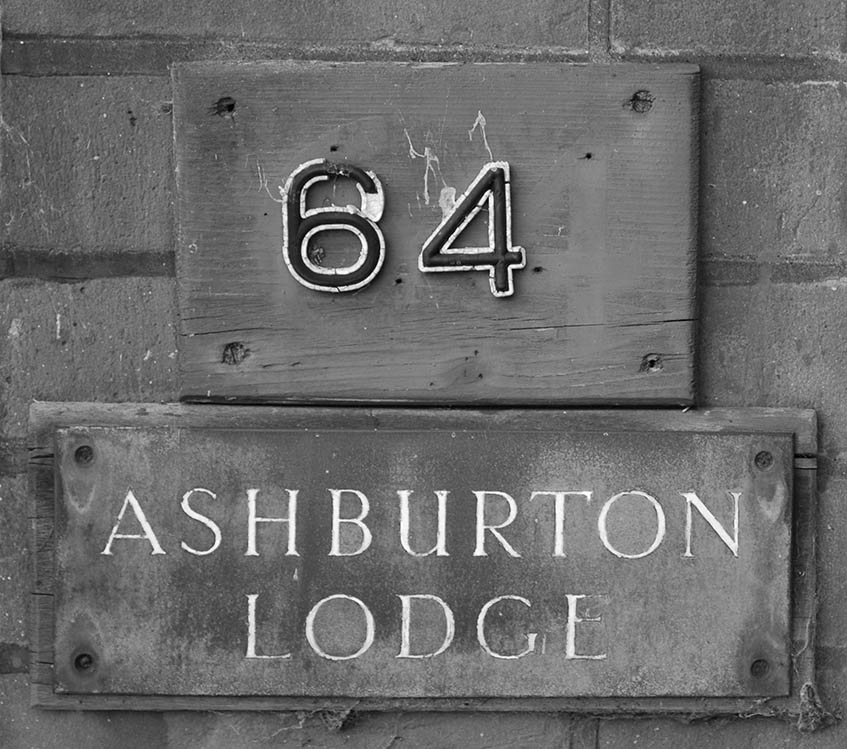
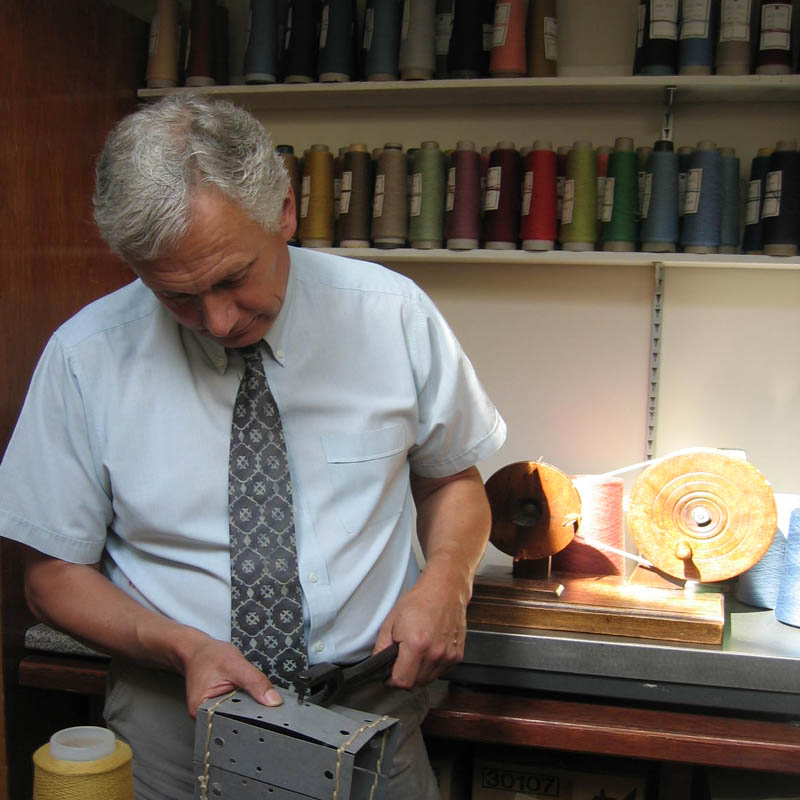
2010s
Although not offering a formal apprenticeship Richard’s connection to the Worshipful Company of Weavers, its textile committee and entry to work scheme gave Richard the opportunity to take on Woven Textile Design graduates from the top universities. This experience of warping, handweaving and design is the perfect grounding for learning the specialism of historic fabric reproduction and designing bespoke contemporary fabrics from scratch. Through this decade Richard trained three graduates, of which Natalie Mumford is now director.
Expertise in custom colour development and bespoke dyed projects continued alongside expanding capabilities in creating special fabrics from an extensive range of stocked yarns continued to see private projects for decorators and renowned brands thrive. Alongside historic recreation projects for Dumfries House, Northumberland Estates, St Giles House, Brighton Pavilion and Hillsborough castle, Humphries Weaving modernised its branding and was an early adaptor of social media.
In 2018 they were honoured to receive a Royal Visit from HRH The Princess Royal in her capacity as the President of UK Fashion & Textiles Association (UKFT). During her 35 year tenure she has been a passionate supporter of the UK fashion and textile industry and a great champion of the innovative, skilled and creative individuals and companies within it.
Shortly afterwards Humphries Weaving supported a National Lottery funded project to document video, oral and written histories about the weaving history of Sudbury, the companies along with the lives and stories of the people who build their careers in the industry. The project includes recorded interviews with Richard Humphries, Natalie Mumford and Brian Turner (Retired). https://www.sudburysilkstories.org/about
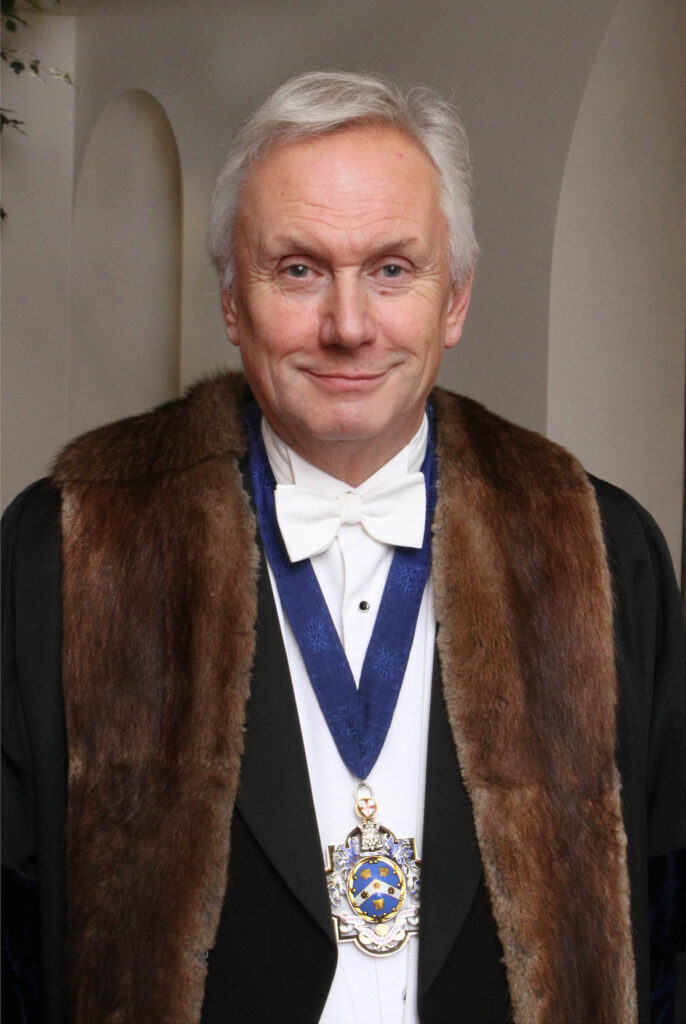
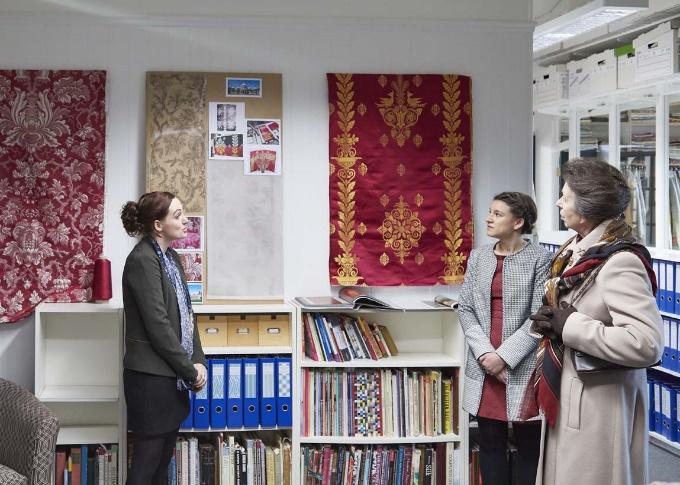
2020s
In 2022 Humphries Weaving proudly celebrated 50 years with a series of celebration talks, bringing together customers, colleagues and friends of the business in celebration at Spencer House, London and Gainsborough House, Sudbury.
They were part of the first UK Mill to achieve OEKO-TEX® STeP certification for sustainable textile production. This accreditation rewarded the company for their regard of environmental protection, social responsibility and commitment to sustainable production conditions.
In 2025, Humphries Weaving was given the King’s Award for Enterprise in Sustainable Development. This award recognises outstanding businesses and is the most prestigious business award in the country. The mill works on reducing its carbon footprint and environmental impact, sourcing responsibly and eliminating waste; including recycling 100% of all textile by-products.
The fabrics created receive accolades from historic bodies, RIBA and the interior design world. With custom dyed yarn capabilities and stocked range of yarns at their fingertips, the team continue to flex between pushing the technicalities of contemporary fabric design whilst retaining the character and integrity of historic recreation.
Today the company consists of 3 talented account managers who continue to advise and project manage bespoke fabric developments to the world’s most prestigious clients and are proud to be continuing to work with the clients listed throughout our milestones as well as with new markets across the world.
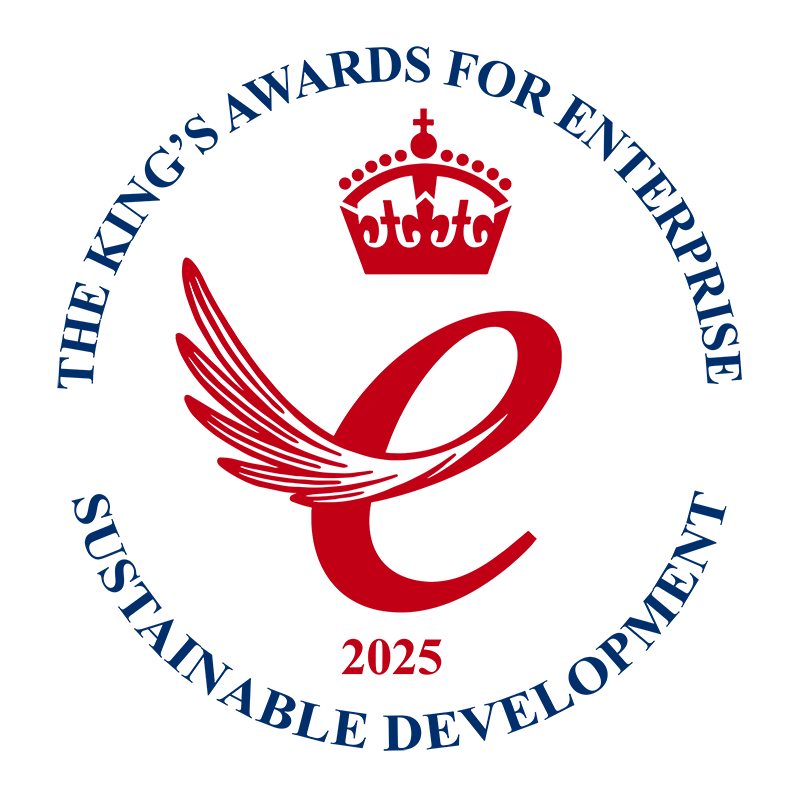
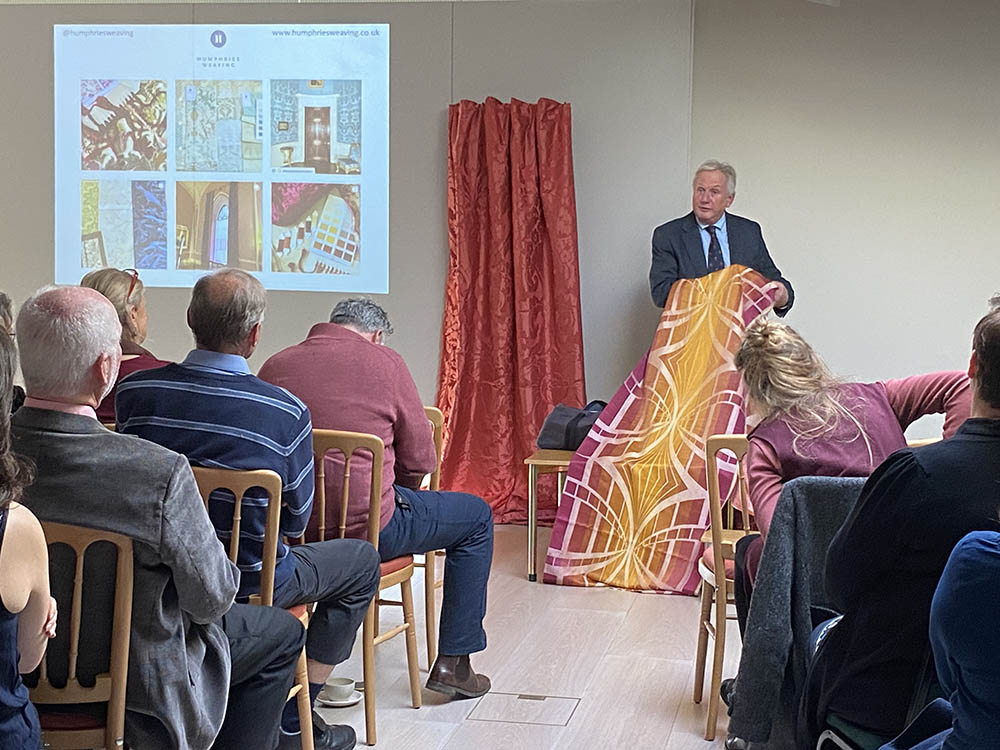
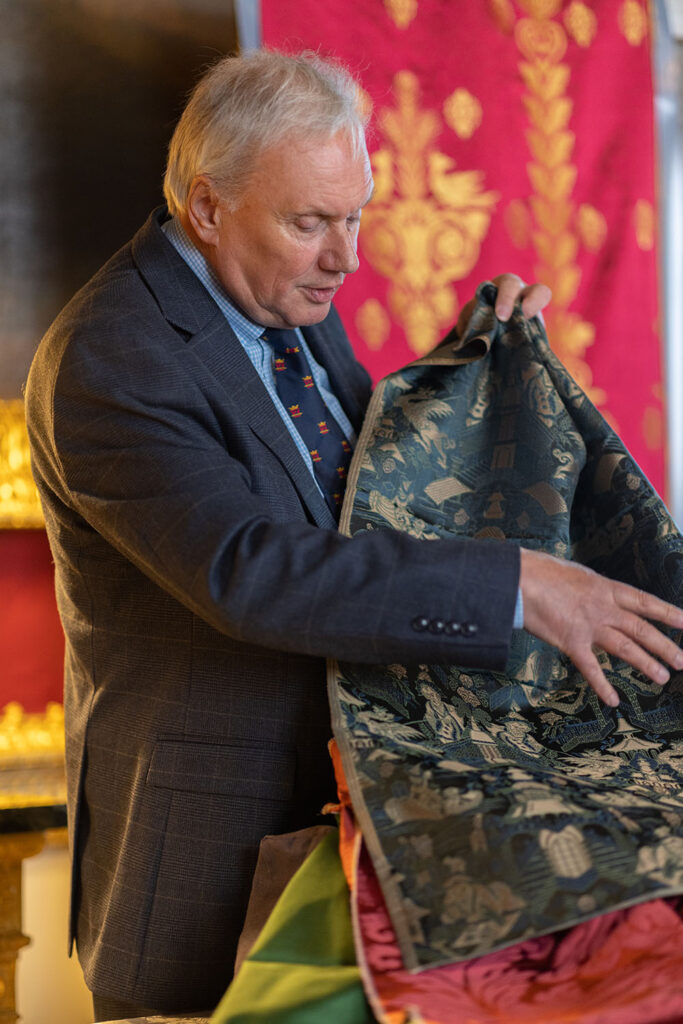