High Tech Solutions to Dyeworks Sustainability
Humphries Weaving continues to make improvements in all aspects of quality and sustainability in its manufacturing processes, here we share some background to dyeworks sustainability. One of the areas that has taken much of our focus has been in the dying area. The majority of the yarns dyed and woven at Humphries Weaving are natural fibres. Silk, cottons and wools are the yarns most often utilised and being 100% biodegradable, are ultimately some of the most sustainable fibres to dye and weave.
Yarn dying, as with all dying processes, uses large amounts of water, power in the form of heating, and chemical dyestuffs. The dye works at Sudbury Silk Mills in 2009 was updated with all new equipment utilising state of the art technology. This department with its development lab, modern dye kitchen and pressurised cone-dying vats is an ultra-efficient area. Dying on re-usable cones, reduces waste and pressurised vats reduces the amount water required in the dying process. The heat from the liquor is recovered to preheat water for subsequent dying’s, which in turn cools the waste liquor to a temperature required for treatment.
As a company we are 100% REACH compliant. In 2007 the EU directive (EC) 1907/2006 came into force. This “Registration, Evaluation, Authorisation and Restriction of Chemicals” directive controls what chemicals can be used within our dyeworks and these regulations are updated on a regular basis. This makes both the working environment and our end product fully compliant and safe.
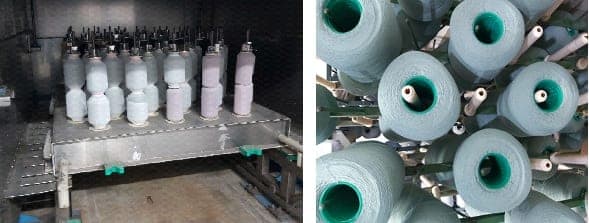
Left: Yarns drying in our Radio Frequency drier & Right: Custom dyed silk yarns ready for re-winding
However, the most challenging aspects of sustainability is the effluent that remains at the end of the dying process. Waste water treatment normally consists of a mixture of physical filtration, chemical and biological treatments. However, with these traditional processes, there always remains resides or slurries, that need to be collected and disposed of.
It was identified that an advanced technology was being developed in Cambridge Science park for use in the cleaning of contaminated drinking water in under-developed countries. Having worked with the technology supplier to adapt this for our purposes, two Hydroxyl Radical Treatment modules were incorporated into our dyeworks.
This process involves passing the used dye liquor over boron plates that are impregnated with industrial diamonds. A fluctuating charge is passed though the plates and this creates Hydroxyl Radicals which oxidises 100% of the organic dyestuffs, turning them back in to the elements from which they are created – oxygen, nitrogen and hydrogen. This results in completely clear and pure water and a small amount of hydrogen. There is no resultant slurry to dispose of.
The pure water is then discharged into the sewers which is ultimately reprocessed and recycled.
Sudbury Silk Mills was one of the very first textile manufactures to utilise this technology and is always looking to make sure that we are aware of further developments and other solutions to improving sustainability.